Compounding HD CSPs: Reducing Risk of HD Exposure from Compounded HD CSPs
- Steve Milstead, PharmD, BCSCP
- Mar 11, 2023
- 6 min read
Updated: Apr 10, 2023
Reducing risk of exposure from trace hazardous drugs is an important process to integrate in your daily routine when handling hazardous drugs (HDs). For sterile compounding of HDs, reducing risk of exposure involves strict adherence to processes that ensure all CSPs and materials used to compound remain contained and decontaminated prior to removing form the containment primary engineering control (C-PEC). However, the mitigation process begins prior to the HD making its way to the C-PEC for manipulation.
This post will focus on the containment strategies and best practices for receiving sterile HDs that requires manipulation, the compounding of the sterile HD and the delivery of the HD CSP to the end user. Remember, USP <800> goes beyond just compounding of hazardous drugs (sterile and nonsterile) and includes all aspects of handling from receipt to waste of HDs.
It has been shown that HDs packaging is contaminated with HD residues from the manufacture. These residues can be traced throughout transport and delivery to the facility. It is important that HD packaging is deactivated and decontaminated with an HD decontamination agent (e.g., oxidizer) upon receipt to avoid contamination throughout the facility from trace HD residues (remember to use proper PPE during receipt; ASTM-rated gloves and when items are not in sealed plastic bags, a multi-gas cartridge and p100 filter would be best practice).
Often contamination isn’t visible but very much present and precautions are necessary. The photo below represents an obvious contamination issue from the manufacturer.
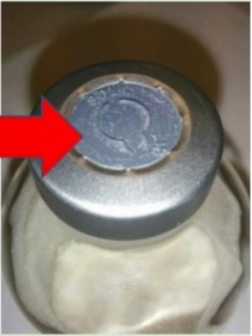
For simplicity of this blog post, HD will refer to the following:
Antineoplastic drugs on table 1 of NIOSH that require manipulation.
Any hazardous drug active pharmaceutical ingredient (API)
Any other NIOSH hazardous drug without an assessment of risk (AOR) in place – the AOR may exempt the HD from certain containment requirements if deemed safe by the facility.
Any HD that is new to the market or not evaluated by NIOSH and do not have and AOR in place.
Any investigational drugs without manufacturer information concerning the hazards of the chemical.
HDs are received in a neutral or negative pressure receiving area. Prior to placing an HD in stock, the HD’s outer container must be wiped down with an HD decontamination agent and the wiper discarded in an approved trace HD waste container. Once it is decontaminated, the HD is ready for storage under negative pressure. The facility may have a dedicated negative pressure storage room for HDs or, if the facility does not manipulate any HD APIs and they have AOR in place for other HDs, some may choose to store HDs for sterile manipulation in the negative pressure buffer room. No matter which storage situation the facility has in place, upon receipt of an HD the outer container will always be wiped down with an HD decontamination agent to remove any obvious or potential HD residues left behind from the manufacturer and discard the wiper used for cleaning in the trace HD waste container.
However, it is important to remember USP <797> applies if the storage area will be the negative pressure buffer room. If this is the case, it will be required to wipe down the item with either a sporicidal agent, EPA-registered disinfectant or sterile IPA 70% and cleaning wipers discarded in trace HD waste container. The best practice for introducing any item into a controlled environment is to use a one-step sporicidal disinfectant cleaner to ensure integrity of your environment. Note: There are decontamination agents that are also one-step sporicidal disinfectant cleaners that can be used to streamline your processes effectively.
Once a product is ready to be used in compounding:
If stored in an unclassified negative pressure storage room, it will be cleaned with either a sporicidal agent, EPA-registered disinfectant, or sterile IPA 70% (keeping in mind that a one-step sporicidal disinfectant cleaner is best practice). If the product is stored in an original container (e.g., vial in a box), the item will be removed from the original container and decontaminated with an HD decontamination agent followed by the disinfection process just mentioned prior to introducing into the controlled compounding environment. Then before placing the HD in the C-PEC for compounding it will be wiped down with sterile IPA 70%.
If the HD buffer room is used for storage of HD drugs, then it would have already been decontaminated and disinfected prior to storage. Sterile IPA 70% will be used to clean the item prior to placing inside the C-PEC.
A closed system transfer device (CSTD) is strongly recommended for compounding since they have been shown to decrease contamination of the work area. Additionally, administration of IV antineoplastic drugs with a CSTD is required therefore it makes sense that they should be used during compounding so that the end user will have the parts needed for a true closed system from the start. (Note: Prior to using CSTD for compounding or administration ensure compatibility of the drug with the CSTD used. Many of our hazardous drugs can cause destruction/melting of common materials used to make CSTDs).
Once compounding is complete and before removing the CSP from the C-PEC, the final HD CSP is wiped down with a sterile decontamination agent. Then outer gloves are removed and discarded in a sealable bag designated for waste inside C-PEC. Then the final CSP is wiped once more with the sterile decontamination agent and removed from the C-PEC, labeled and place in a sealable HD containment bag for delivery.
Remembering that there are great choices of one step sterile decontamination agents that are also cleaner disinfectants, the C-PEC is cleaned using sterile decontamination disinfectant cleaning agent twice (ensuring dwell time is observed on second pass for disinfection). Again, outer gloves removed (and, if used, sleeve covers) and discarded in C-PEC designated sealable waste bag. The waste bag is wiped with the sterile decontamination agent and removed to discard as trace HD waste. Then as in any PEC used for sterile compounding, application of sterile IPA 70% follows to remove cleaning agent residues.
The gown and outer shoe covers are doffed and discard in negative pressured buffer room in a waste bin dedicated for trace HD. Upon exiting the negative pressure buffer room all PPE is discarded in anteroom and the employee must wash their hands with soap and water. No PPE may be reused after compounding HDs, not even the gown worn underneath the chemo gown in the negative pressure buffer room. (Note: To avoid double gowning, USP <800> does not mandate doffing the chemo gown in the negative pressure buffer room. However, it strongly recommends doing so which would require double gowning for compounding of hazardous drugs to avoid ungarbed personnel in the HD buffer room).
Although decontamination of surfaces in negative pressure rooms (walls, ceilings, etc.) is not a requirement, it is best practice to do so during monthly cleaning. However, it is important to decontaminate and disinfect surfaces daily (when room is in use) in the negative pressure buffer room that come into frequent contact with final CSPs or any HD that is used during compounding.
After the compounding an HD CSP it is important to remember the safety of the employee transporting the HD CSP and the end user that will be handling it. The final HD CSP must be transported and delivered in a sealed HD-block bag by a trained employee gloved with ASTM-rated chemo gloves. Further handling of the final HD CSP must also be done with ASTM-rated chemo gloves to ensure any residues inadvertently left behind are not transported to the skin. Additionally, even when effective decontamination of the exterior is in place, certain chemicals can still pass through the container over time. Certain containers, such as PVC, protects the product from microbial contamination but chemicals are smaller than bacteria and can easily move through the container contaminating the person delivering, others in contact with the final CSP and surfaces.
The photo below demonstrates movement of chemicals through PVC from betadine being injected into a normal saline PVC bag and placed on white paper. The paper turns black from chemical passing through the PVC barrier onto the white paper. The final CSP container prevents microbes from entering the CSP, but chemicals are smaller than bacteria and may pass through the container under the right conditions.
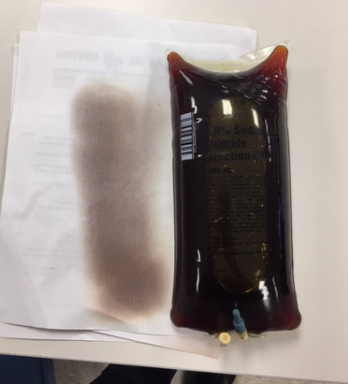
Precautions to prevent HD contamination during compounding are extremely important but additional precautions are needed prior to and after compounding. It is important to ensure processes are in place to protect all employees who encounter hazardous drugs from receiving, to compounding, delivery, administration, and waste of the CSP prepared.

Don't forget to go back and like this post on LinkIn: https://www.linkedin.com/posts/stephenmilstead_compounding-hd-csps-reducing-risk-of-hd-activity-7040492815620988928-7h9o?utm_source=share&utm_medium=member_desktop
Thank you for visiting my site. For more information please visit www.SoignerSolutions.com or email me directly at smilstead@SoignerUniversal.com
Comments